FAQ
Questions and Answers
We have collected answers to frequently asked questions related to the Full Electric line-up.
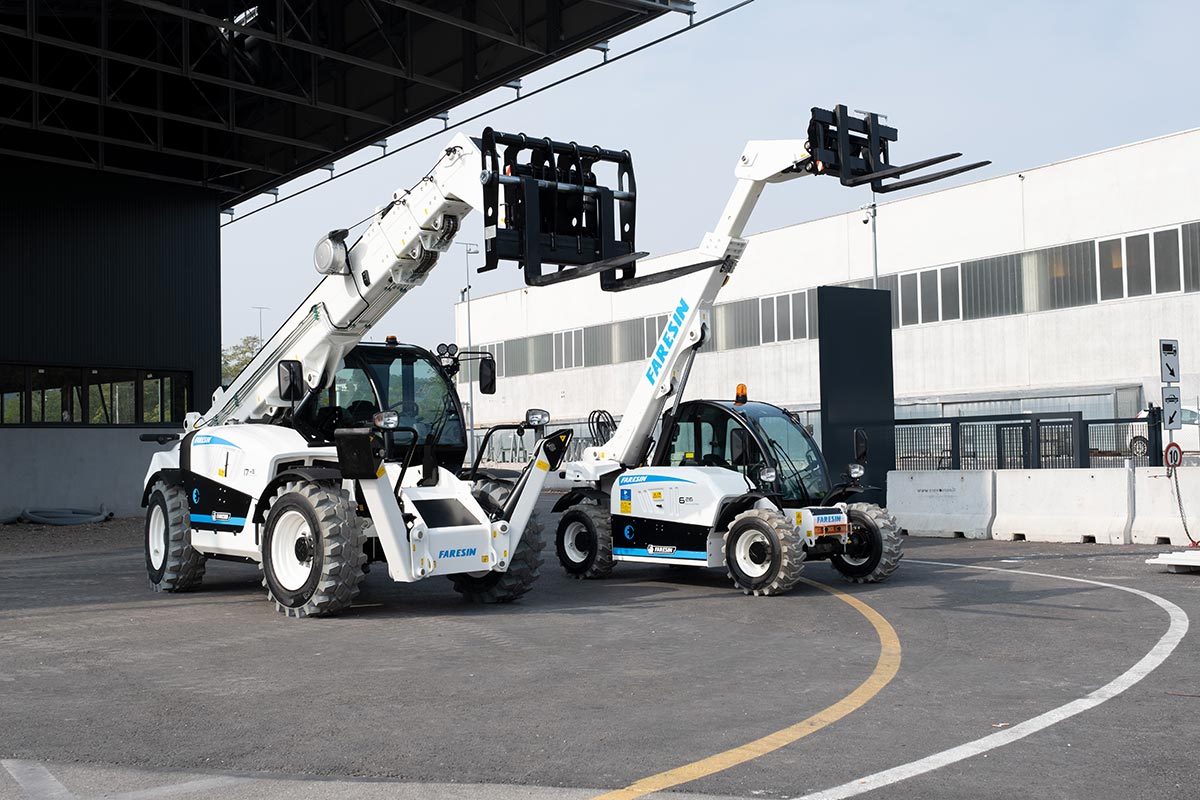
FULL ELECTRIC machines are 100% electric and are equipped with two electric motors: one for traction and one for arm movements.
- 6.26 FE: The machine is fully electric, and can mount a 315 or 420 or 560 Ah battery pack to power two electric motors, one for the transmission rated at 20 kW and one for the hydraulic services rated at 10 kW.
- Big Range FE: The machine is fully electric and has a 105 Ah battery pack to power two electric motors, one for the 51 kW rated transmission and one for the 22 kW rated hydraulic services.
Depending on battery capacity, the range with continuous intensive cycle can vary from three to six hours while the range with standard cycle can vary from six to eleven hours.
Many factors can affect range, including: initial battery charge, environment, weather conditions, weight, accessories, friction, driving style, load, route characteristics, and use of features such as air conditioning. As a result, official range figures may vary further and differ from the figures stated in the data sheets.
- 6.26 Range with continuous intensive cycle in Eco mode can reach 3h with 315 Ah battery, with 420 Ah battery can reach 4h, with 560 Ah battery can reach about 6 hours.
- Big Range: Range with continuous intensive cycle in Eco mode can be up to 4h with 105 Ah battery.
The machine is already optimized to minimize consumption, some adjustments can be made in the way the machine is used, which can limit battery use.
If not used for more than 10 minutes, the telescope will turn itself off. It is advisable to keep the vehicle on charge during long periods of parking, with the standard charger (not Fast). It is advisable to keep the vehicle on charge during long periods of parking, with the standard charger (not Fast).
Energy recovery occurs under braking and when the accelerator is released and is automatically activated. Electric motors act as a generator by converting much of the machine’s kinetic energy into electricity, which is stored in the battery, increasing its range. So whether you are braking, or simply lifting the pedal off the accelerator, the battery can be partially recharged with this energy that would otherwise be lost. The regenerated energy becomes significant when traveling long downhill stretches.
The 6.26 FULL ELECTRIC telehandler with a standard cycle consumes an average of 6.4kWh of energy; the same model equipped with a diesel engine consumes 3.5l/h of fuel, which corresponds to about 15 kWh of energy, with the same duty cycle.
In energy terms, therefore, the FULL ELECTRIC model is much more efficient.
The endothermic engine has been replaced by two electric motors, one for traction and one for services, powered by a lithium-ion battery pack located in the engine compartment.
- For the 6.26 FULL ELECTRIC, the differences from the diesel model are:
The endothermic engine has been replaced by two electric motors, one for traction and one for services, powered by an 80 V lithium-ion battery pack located in the engine compartment.
The 20 kW electric motor for traction was mounted on the front axle.
The electric motor to drive the 10 kW hydraulic pump was mounted on the rear end. - For the Big Range Full Electric Range, the differences from the diesel model are:
Endothermic engine replaced by a lithium-ion battery pack.
An electric motor was mounted on the front axle for traction (51 kW transmission motor).
Another electric motor was mounted to drive the hydraulic pump (hydraulic service motor 22 kW).
The battery is designed in such a way as to make the need to replace it entirely highly unlikely. In the circumstance that a battery repair needs to be carried out, the replacement should be done by trained and authorized personnel.
- The life cycle of the battery depends on the way it is handled and the conditions under which it is used.
- The operator can help preserve battery life by choosing traditional charging over fast charging. When using fast recharges, charging the battery to 80% instead of 100% can help protect its lifespan.
From -10° to +40°
0° to +40° by always leaving the machine plugged in with the standard standard charger, checking its condition at least every two months.
- Regarding FR00E, it is not possible, they are not compatible by voltage and connector.
- As for FR04E, it is possible to recharge the vehicle at public charging stations
- FR00E
Speed with 16.5″ wheels (standard) 0-7.4 mph
Speed with 18″ wheels (optional) 0-9.3 mph - FR04E
First gear speed 6.2 mph
Second gear speed 15.5 mph
Advantages over a diesel: no coupons or diesel filters to change.
Interventions on hydrostatics are much more limited; the engine is engaged directly in the axle.
Neither battery nor motors, unlike a diesel, require maintenance.
Get in touch with us
Do you still have questions? You can contact us, at no cost, every day from 8 a.m. to 6 p.m. via call to our International Customer Care service.
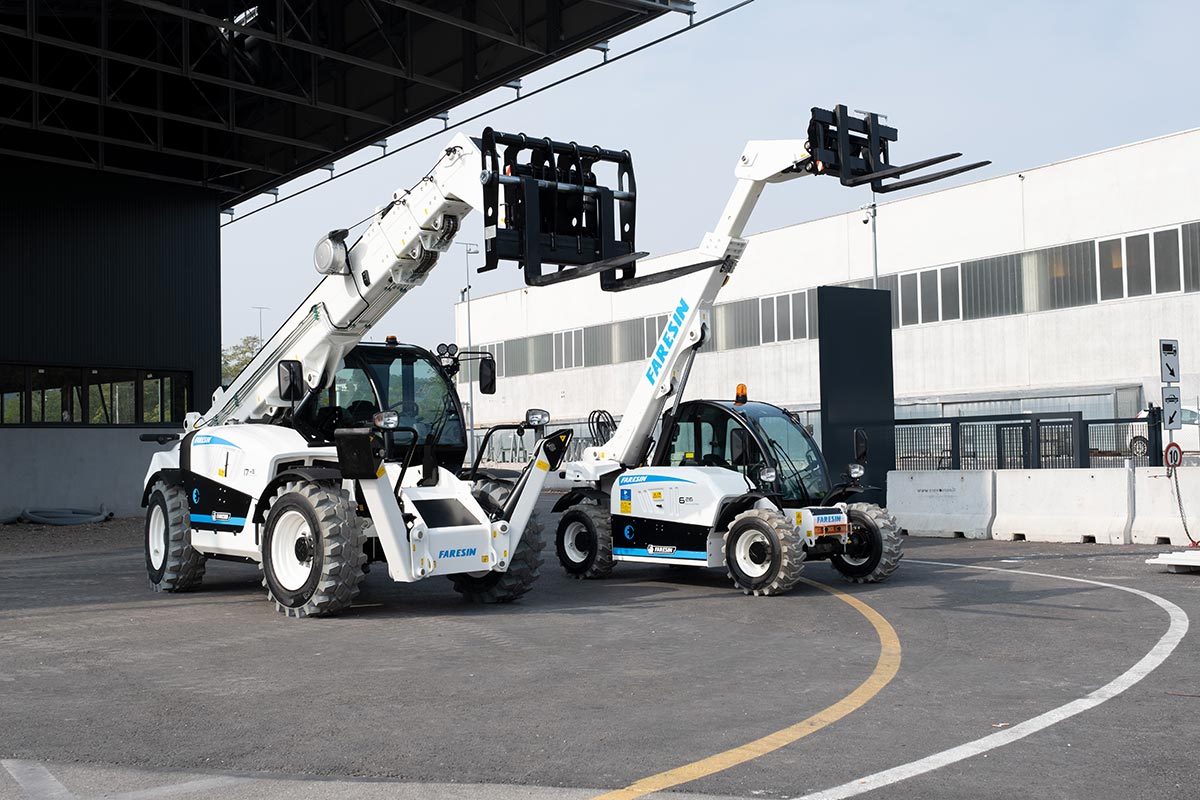